Investment Casting Tolerances
Dimensions, Tolerances, & Surface Texture Information
Investment casting costs are relative to the allowed tolerances for physical dimensions, alloy composition, and need for nondestructive testing. R2 Quality Castings has the affordable investment cast machine parts you need, from marine and mixing propellers to plumbing fixtures and more.
Tolerances
Physical tolerances for investment cast machine parts are governed by several conditions of the lost wax casting process. The temperature of the wax mold and die, the chemical composition of the slurry shell, and the heat treating duration and temperature are just a few factors affecting the size of the final product.
Investment cast parts undergo linear tolerancing for edge straightness, surface flatness, length, hole depth and radii, fillet and chamfer radii, and concentricity. Geometric tolerancing defines and communicates investment casting profiles, parallelism, roundness, perpendicularity, tapering, cam profiles and true positioning.
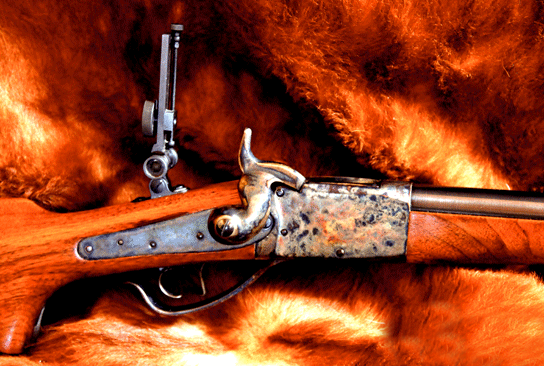
Linear Tolerancing
The R2 Quality Castings foundry normally creates precision investment castings with linear tolerances up to 1” plus or minus .010“, and plus or minus .003” for every additional inch up to 10”. Cast parts larger than 10 inches typically have physical tolerances of .005” per inch. Stricter physical tolerancing is possible with additional straightening and machining.
An exception to the linear tolerance exists on wall thickness where the tolerance must be a minimum of +/- .020”.
Linear Tolerance Chart
Inches | Millimeters | ||
Dimensions | Tolerance | Dimensions | Tolerance |
|
|
|
|
Flatness
Flatness tolerance is the quantified variance from a flat plane. The investment cast part’s surface must lie between the perfectly flat plane and the plane representing the maximum deviation permitted under the design parameters. Machine parts deviating beyond the pre-established parameters will never be shipped by R2 Quality Castings.
Volumetric contraction of cooling wax and metal alloys determines the flatness variance of the final investment cast part. Shrinkage always causes some amount of dishing, though this effect will be mitigated to tolerances by applying specialized investment casting techniques. Flatness tolerances vary significantly with different types of metal alloys and the physical structure of the cast products.
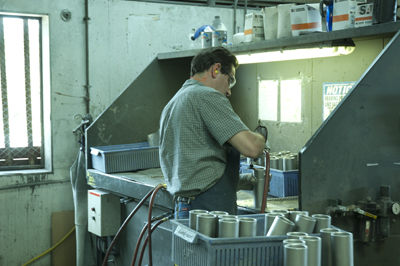
Straightness
Measuring straightness is determining the maximum tolerable diameter of the part’s divergence from a perfectly straight line. Axial straightness of investment cast shafts or plates is determined by our rigorous quality verification process, weeding out propellers and other machine parts before any product is shipped to you.
Some castings are more prone to bending during the cooling process than others. Our investment casting professionals know when a design will bend, but the particular angle cannot be accurately predicted. Constant sections tend to experience an axial bow of approximately 0.024 inches per foot.
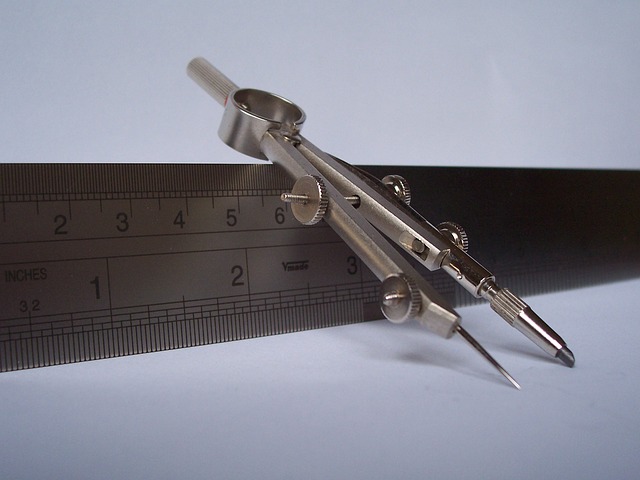
Parallelism
If your design includes parallel prongs supported only at one end, this presents a particular challenge for the completion of precise investment casting. Yoke castings also require special attention. R2 Quality Castings will discuss these types of parts with you prior to production.
Parallelism of these prongs is difficult to maintain due to volumetric shrinkage of the supporting structure. Yoke holes can also deform substantially as they reach ambient temperature. Careful design adjustment for volumetric shrinkage is critical to achieving an accurate part. These work pieces benefit from more extensive tooling and finishing.
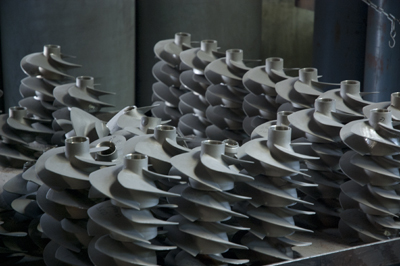
Roundness or "Out of Round"
“Out of round” is defined as the radial difference between a true circle and a given circumference. It is the total indicator reading when the part is rotated 360° or it can be calculated by taking half the difference between the maximum and minimum condition. The latter technique is usually preferred since it takes less time.
The difference between minimum and maximum radii of a circular part gives us the measurement of its roundness. The degree to which an investment cast component lies out of round is strictly controlled by R2 Quality Castings’ detailed inspection process. Our investment casting foundry does not ship parts falling outside established tolerances.
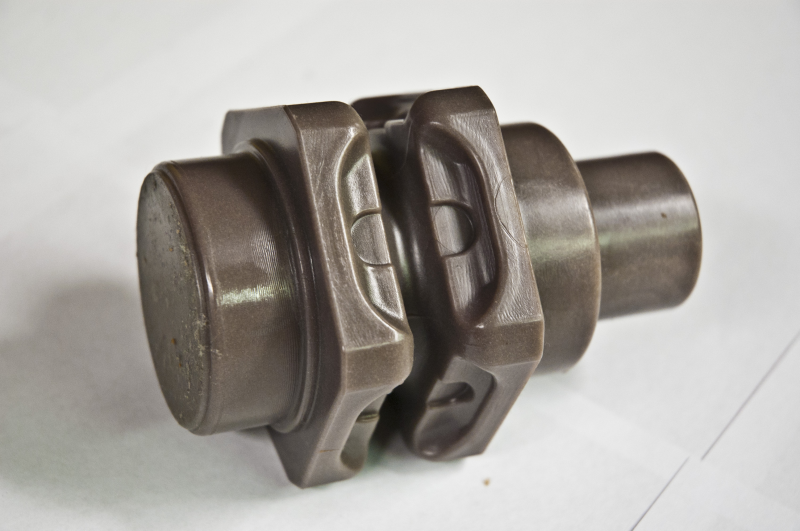
Concentricity
Concentricity of cylindrical surfaces is measured by the distance between their axes. Precise concentricity is essential in a wide variety of machines, often to reduce vibrations caused by rotating components. In these cases, above-tolerance eccentricity can be the root cause of gradual vibrational wear and tear to surrounding machine parts. R2 Quality Castings’ thorough quality verification process prevents defective parts from shipping with your order.
Shafts and tubes must not only be concentric, they must be extremely straight. Straightness correlates with concentricity; the ends of each piece may be true circles, however a lack of straightness will directly affect the concentricity. Our investment casting foundry ensures each part is within the bounds of acceptable concentricity, providing you with the best quality casting components.
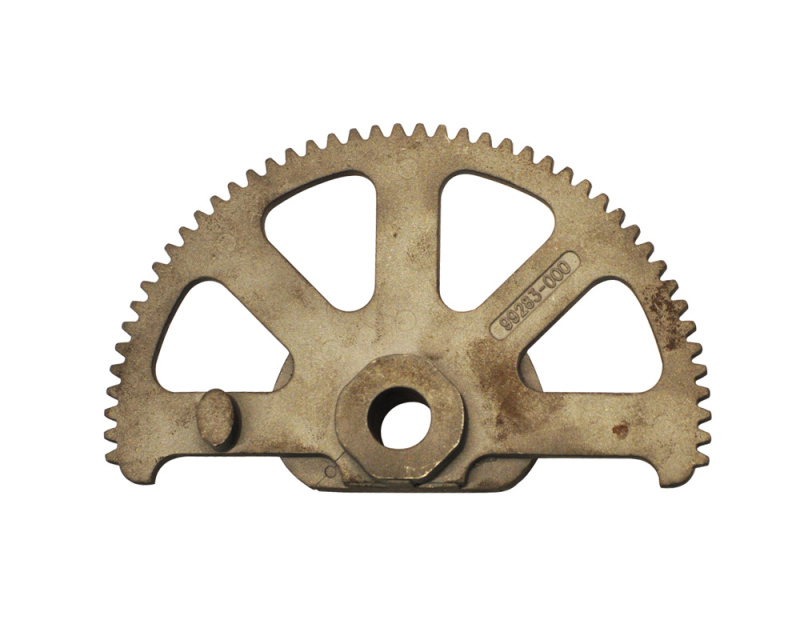
Hole Tolerance
Hole tolerance refers to the necessary roundness of a cast hole. The surrounding metal must be symmetrical to provide proper fit and/or clearance. This is extremely important for cast parts which fit together, like wheel shafts, to ensure it will fit tightly without vibration. Longer holes can experience more internal concavity, such that the interior hole diameter is greater than that of the openings. Care is required to meet specified tolerances.
Hole tolerance ensures interior shrinkage, and clearance is +/- .003” for up to ½ inch diameter holes, to provide an accurate shape and fit.
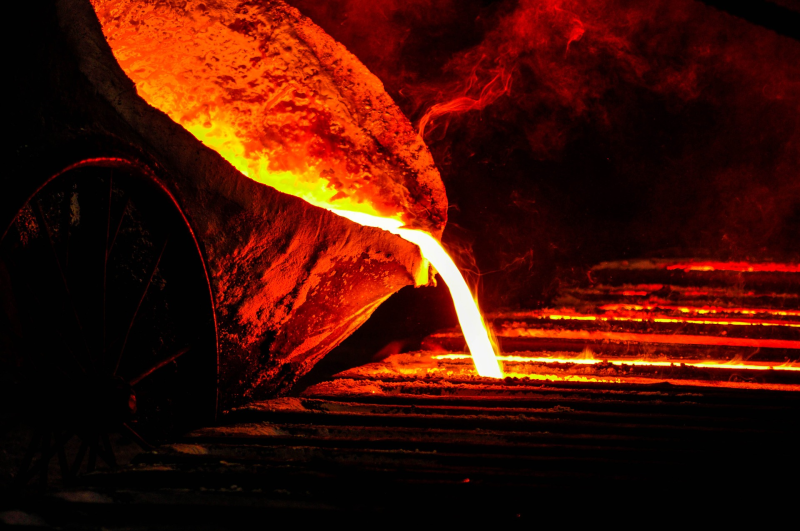
Curved Holes, Internal Radii & Fillets
Curved holes can be created by preformed ceramic cores or a soluble wax. The normal hole tolerance will be doubled to take the curvature into account and all dimensions’ tolerance will be multiplied by two. We cannot size these holes so we provide a diameter tolerance of +/- .005.” Internal radii and fillets should have as wide a tolerance as possible as they are difficult to control and measure.
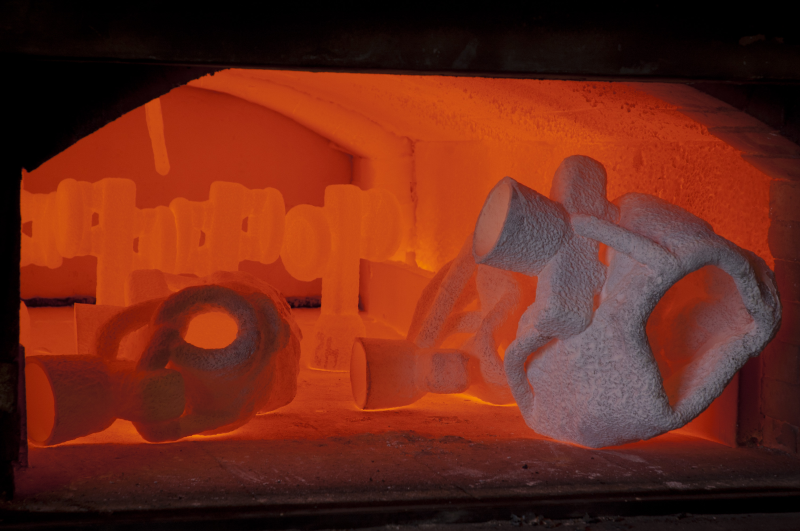
Casting Within Tolerances
R2 Quality Castings offers superior investment casting services with tolerancing to ensure each casted component is to the necessary specifications. We hold to strict standards to ensure our investment casting process is accurate and test each part to confirm each aspect is within the above measurements. With our investment casting foundry, you’re sure to have the most accurate, high quality metal castings.
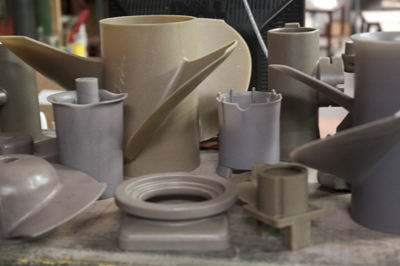